Infrared and Ultraviolet Diagnosis of Composite Insulator Core Rod Defects
Composite insulators are currently used in a huge amount, but when the mandrel process is not well controlled, defects will be left, and string breaks and breakdown faults will continue to develop during operation. In order to eliminate the fault in the bud, the diagnosis of composite insulator mandrel defects is very important. For the operating unit, the live detection method is the best method for both reliability and equipment status perception. At present, the relatively effective and mature methods for the live detection of composite insulators are infrared and ultraviolet tests.
1. Infrared diagnosis of internal defects

1.1 Infrared features of internal defects
The heating sources of composite insulators mainly include polarization loss, partial discharge, and leakage current. The former two are due to the excessive concentration of the electric field caused by the defect; the leakage current heating is mostly caused by the deterioration of the canopy of the insulator, and the leakage current is concentrated in the deteriorated part, and there is an obvious temperature difference with the surrounding area. Usually, the end of the air gap and carbonization channel will become a “hot spot” due to the existence of partial discharge, while the middle part of the carbonization channel is often at a lower temperature due to the weaker electric field.
Example 1: Wet ends
A 500kV line has multiple composite insulators with a temperature rise of 2-4K . The temperature rise test under AC and DC withstand voltages is carried out in the laboratory, and the applied voltage amplitude is equal to the maximum operating voltage amplitude ( 1.1Um/ ).
Features: When AC high voltage is applied, the temperature rise under high humidity is about 4-5K , which is significantly higher than that under low humidity. In the DC high voltage test, the temperature rise of the insulator is hardly observed; the difference in temperature rise under different humidity makes the on-site During detection, sometimes the temperature rise is high, and sometimes there is no temperature rise. (Reference: Influence of moisture on composite insulator sheath on abnormal temperature rise at the end)
Example 2: Carbonization channel
One of the double V- string composite insulators in a certain tower of a 500kV line was broken. There were many holes in the core rod of the broken insulator, and electric corrosion channels had been formed inside. The broken insulator A and the same batch of insulators B were placed under the operating voltage for infrared measurement. temperature.
Infrared temperature measurement of two insulators


▲Figure 1 Insulator A (fracture) infrared characteristic map
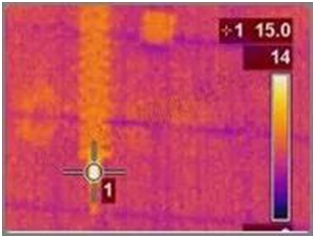
▲Figure 2 Infrared characteristic diagram of insulator B
The detection found that The middle temperature of insulator A is 14.8 ℃, which is higher than that of insulator B 12.9 ℃. During the test, it was found that the temperature of units 45-46 in the middle of insulator A ( the first unit at the low-voltage end is the first unit , and the junction point between the corroded and uncorroded mandrel between units 45-46 ) is higher than that of insulator B 1.9 ℃ 1 ) The temperatures of the high-voltage ends of insulators A and B are both around 15 ℃, with little difference.
Infrared signatures of insulators with galvanic channels:
①The boundary area between the high voltage end of the electro-corrosion channel and the intact mandrel is an area with obvious temperature rise;
②Compared with insulators without electro-corrosion channels, the temperature rise may not be high (only 1.9 °);
③The temperature difference between different positions of the insulator itself is more obvious;
(In fact, the B insulator also has internal defects and poor bonding)
1.2 Test Judgment
The judgment criteria for infrared diagnosis of composite insulators in operation on site is the appendix I.2 of the standard ” DL/T 664 Application Specifications for Infrared Diagnosis of Live Equipment”. When the temperature difference of composite insulators exceeds 0.5-1.0 K , attention should be paid.
Considering that on-site infrared detection is easily affected by external light reflection, angle, and focus definition, and the test error is difficult to control, many units (including China Electric Power Research Institute and provincial companies) currently relax the above criterion to 2.0K during on-site tests .
In order to assist the judgment, for suspicious insulators, multiple follow-up inspections should be carried out, and phase-to-phase comparisons should be carried out to assist judgment.
1.3 Test Notes
a. Avoid the influence of sunlight and other visible light
Since the composite insulator is a voltage-induced heating device, its temperature field test is easily affected by the external environment. When the sunlight and visible light are strong, it will cause the temperature difference between the sunny side and the back side of the insulator, and cause the temperature difference between the different sides of the mandrel. As shown in Figure 3, the outside sunlight was strong during the test on that day . At this time, the highest point of infrared temperature measurement was located on the surface of the shed with strong sunlight reflection. They are 27.9°C and 25.0°C respectively, and the temperature difference reaches 2.9 K. The temperature difference caused by sunlight is very likely to submerge the possible hot spots inside the mandrel, resulting in missed judgments. Therefore, when testing, it is best to carry out on a cloudy day.
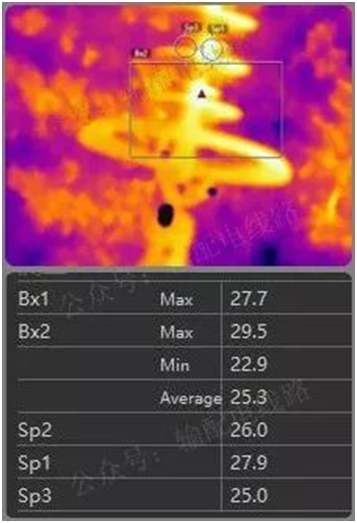
▲ Figure 3 The impact of sunlight
b. Reasonably set the test distance, reflectivity, wind speed and other parameters. The reflectivity should be set between 0.85 and 0.95. The test distance should be set reasonably when climbing the tower and testing under the tower (you can carry rangefinder, anemometer and other equipment to survey the test environment. parameter);
c. Try to choose the angle perpendicular to the insulator mandrel during the test, and pay attention to the focus at the same time. For the infrared photos that are too blurred, they should be discarded. The temperature rise should be determined by comparing the hot spot of the insulator mandrel with other farther positions of the mandrel, as shown in the figure below:

▲ Figure 4 Recommended shooting angles
d. Record the time, ambient humidity, and temperature during the test, and give infrared photos for subsequent analysis.
e. When it is found that the infrared photo test parameters are set incorrectly, the software of the general infrared instrument has the inversion function of the test image. Using the software to modify the test parameters and recalculate the temperature rise can reduce the error caused by incorrect test parameter settings to a certain extent. impact (but still less accurate than if the parameters were set correctly when actually testing).
f . When the tower is too high, the test distance is long, and the resolution of the infrared instrument is limited, so the temperature rise cannot be measured. The test distance can be increased by adding a focusing lens.
2. Ultraviolet diagnosis of internal defects
2.1 UV characteristics of internal defects
When corona is caused by defects such as carbonization channels and erosion of composite insulators, the corona can be observed by using an ultraviolet imager. The advantage of the ultraviolet method is that the detection distance is long, the detection sensitivity to corona is high, and it is beneficial to detect defects as soon as possible, and the detection sensitivity to continuity defects is higher than that of the infrared method. The disadvantage of the ultraviolet method is that the types of defects that can be detected are relatively limited. Not all defects generate stable coronas. For example, cracks on the surface of mandrels will only generate coronas after being damp, but at this time raindrops on the surface of insulators may also generate coronas. The ultraviolet method has certain requirements on the light and the detection position. The discharge image can only be obtained on the front of the discharge. Therefore, the ultraviolet method is mainly in an auxiliary position for the judgment of the local defects of the insulator, and is usually used in conjunction with the infrared method .
UV detection case:
A 500kV transmission line composite insulator found a temperature rise, and carried out infrared and ultraviolet tests at the same time, as shown in the figure below.
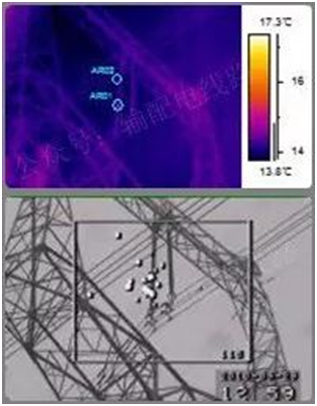
▲ Figure 5 UV spectrum of composite insulator with galvanic corrosion channels
The ultraviolet images of the composite insulator when the sheath is damaged, the sheath is cracked along the mandrel, and the end is creeping are shown in Figure 6-Figure 8.

▲ Figure 6 The ultraviolet spectrum of insulator partial sheath damage

▲ Figure 7 The ultraviolet spectrum of insulator partial sheath damage
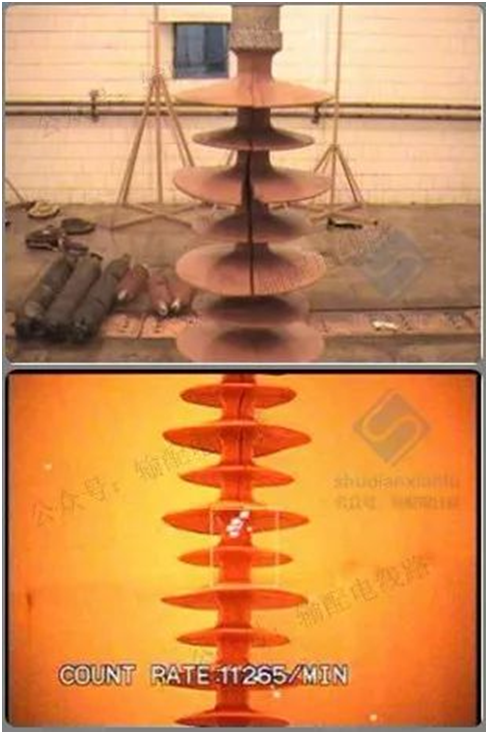
▲ Figure 8 Severe contamination caused creepage on the surface of the end
UV characteristics of defective insulators:
①For the insulator with the mandrel broken, when the infrared and ultraviolet are detected at the same time, the area where the insulator has abnormal discharge is consistent with the area where the temperature rise exceeds the standard; ( if there is a temperature rise and ultraviolet discharge at the same time, the probability of defect is very high)
②The partial sheath is damaged, and there will be significant ultraviolet discharge at the end of the elongated crack of the sheath;
In addition, the end creepage caused by serious local pollution will also cause damage to the insulator sheath. For composite insulators, if the ultraviolet test finds that there is concentrated and stable discharge on the surface of the sheath, the possibility of damage to the sheath should be considered, and careful inspection is required. If the sheath is damaged, it should be replaced as soon as possible.
2.2 Test Judgment
UV test is based on the standard: ” DL/T 345-2010 Guidelines for the Application of Ultraviolet Diagnostic Technology for Live Equipment”;
Diagnosis methods include the judgment of the equipment itself and the comparison and judgment between three-phase equipment. Generally, when the discharge is severe, the value of ultraviolet photons is relatively large, which is easy to judge. Follow up detection and carry out phase-to-phase comparison.
2.3 Notes on testing
① Set a reasonable gain
When the gain setting is too low, the detection sensitivity is not enough, and if the setting is too high, it is easy to be interfered by external optical fibers. Generally, the gain is set to the maximum value when starting the test, and the gain is gradually adjusted according to the saturation of the number of photons;
② The wind speed should not be greater than 5m/s;
When the wind speed is too high, it will affect the number of UV photons observed;
③Avoid shielding and electromagnetic interference;
④ It is advisable to test at night or on cloudy days;
⑤Excessive pollution on the surface and loss of hydrophobicity of composite insulators will also produce ultraviolet signals, which need to be distinguished;
3. Summary
① For insulators suspected to have mandrel defects, infrared and ultraviolet inspections can be carried out at the same time. If there are temperature rise and ultraviolet discharge at the same time, the probability of defects is very high;
②Infrared testing needs to set reasonable parameters to ensure the clarity of the test image, otherwise the test results will have large deviations, and the effect of the tower test is significantly better than that of the tower test;
③For the electro-erosion channel, it is often the end of the electro-erosion channel that generates infrared and ultraviolet abnormal signals;
④The temperature rise caused by internal defects is not obvious at the initial stage, and often requires multiple follow-up tests and phase-to-phase comparisons for final confirmation;
⑤UV testing is more sensitive to mandrel damage defects, but mainly relies on infrared testing for internal defects.
#CompositeInsulator#TransmissionLine#linepostinsulator#PinTypeInsulator #CrossArmInsulator#RubberInsulator#ElectricProduction #InsulationProduction #PowerStationProductions#lightingarrester #surgearrester #dropoutfusecutout #dropoutfuse #outdoorisolatingswitch #highvoltagefuse #polymerinsulator #porcelaininsulator #glassinsulator #highvoltagevacuumcircuitbreaker #vacuumcircuitbreaker #pininsulator #postinsulator #crossarminsulator#electricpower#МФЭС#VDNKh#ВДНХ#МЕЖДУНАРОДНЫЙФОРУМ#ЭЛЕКТРИЧЕСКИЕСЕТИ
#sf6 #loadbreakswitch #loadswitch #35kv #ringmainunit #RMU #electrical #switchgear #transformer #manufacturing #design #protection #supply #power #threeworkstations #earth #electricalequipment